
This design is very stable and efficient, and it is perfect for high-speed aircraft. The most efficient airfoil design is the delta wing airfoil. However, it is not very efficient at high speeds, and it can be difficult to control at high angles of attack. This design is simple and efficient, and it is usually used on smaller aircraft. The most common airfoil design is the symmetrical airfoil. There are many different airfoil designs, and each one has its own advantages and disadvantages. What is the best airfoil design?Īn airfoil is a shape that is designed to produce lift when it is moving through the air. The best airfoil for a particular application depends on the weight and speed of the aircraft, the desired flight characteristics, and the material used to construct the airfoil. A thinner airfoil creates less drag and less lift. A thicker airfoil creates more drag, but also produces more lift. The thickness of the airfoil is also important. Longer and narrower airfoils produce more lift and less drag, while shorter and wider airfoils produce less lift and more drag. The length and shape of the airfoil are determined by the desired flight characteristics of the aircraft.
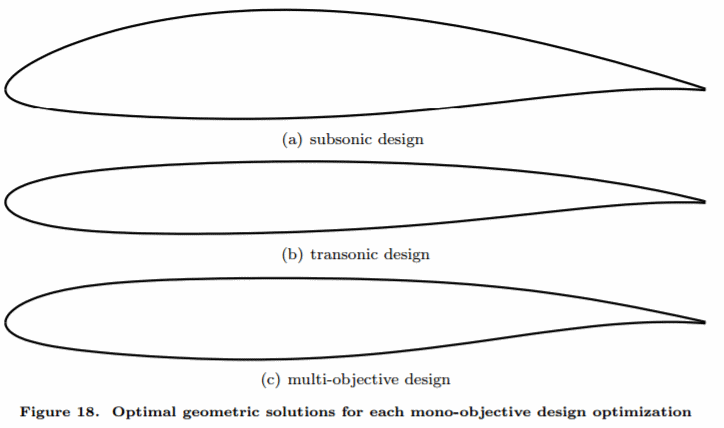
IT IS INTERESTING: Decorating Tiered Trays However, for more advanced applications, it is necessary to use a computer simulation to calculate the aerodynamic properties of the airfoil. Some common airfoil shapes are the NACA 0012 airfoil, the NACA 4412 airfoil, and the NASA 65 airfoil.īy understanding the basic principles of flight and the aerodynamic properties of airfoils, it is possible to design a basic airfoil shape that will produce lift. The best airfoil shape depends on the type of aircraft and the type of flight conditions. A thin airfoil has a low drag coefficient and a high lift-to-drag ratio, while a thick airfoil has a high drag coefficient and a low lift-to-drag ratio.įinally, the shape of the airfoil is also important. A high lift-to-drag ratio is desirable, because it means that the aircraft will require less power to produce lift.Īirfoils are also classified by their thickness. The most important property of an airfoil is its lift-to-drag ratio, which is the ratio of the lift produced by the airfoil to the drag force on the airfoil. The next step in airfoil design is to understand the aerodynamic properties of airfoils. Airfoils are designed to create this curved surface, and they can be either fixed or adjustable. The ideal shape for a wing is a curved surface that can deflect the most air downwards. The shape of the wings is critical in creating lift.

This creates an area of high pressure below the wings, while the area of low pressure above the wings sucks the aircraft upwards. Lift is created by the wings of the aircraft, which deflect air downwards. An aircraft is essentially a flying machine that uses lift to overcome the force of gravity. The first step in airfoil design is to understand the basic principles of flight. However, by understanding the basic concepts involved in airfoil design, it is possible to create a basic airfoil shape that will produce lift. The RAE 2822 case exhibited a drag reduction from 217.79 to 132.79 counts, a 39.05% decrease using BandAids."-Abstract, page iii.How To Design An Airfoil 8 min read Reading Time: 6 minutesĭesigning an airfoil is a complex task that can take many years of experience to perfect. Employing the BandAids technique yields a 78.67% drag reduction, from 473.91 to 99.98.
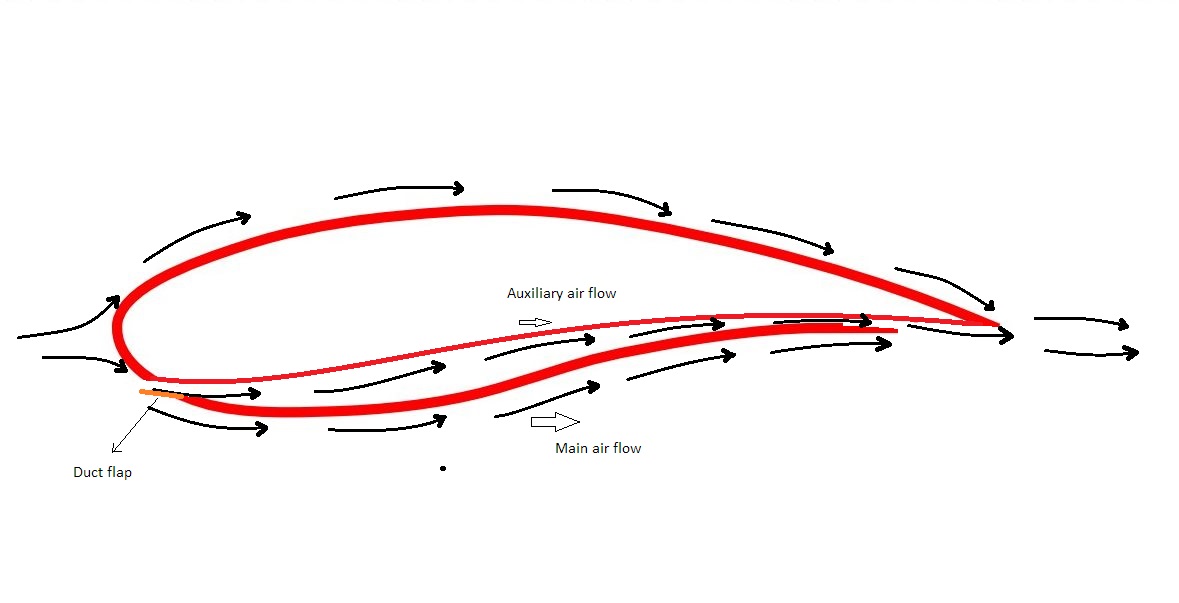
Using the MASSOUD technique, a drag reduction of 72.14% is achieved for the NACA 0012 case, reducing the total number of drag counts from 473.91 to 130.59. The thickness and camber distributions are the local design variables for MASSOUD, and selected airfoil surface grid points are the local design variables for BandAids. For the two airfoil cases, angle of attack is treated as a global design variable. Two shape parameterization techniques are employed to study their effect and the number of design variables on the final optimized shape: Multidisciplinary Aerodynamic-Structural Shape Optimization Using Deformation (MASSOUD) and the BandAids free-form deformation technique.
Airfoil shape code#
The FUN3D CFD code of NASA Langley Research Center is used as the ow solver for the gradient-based optimization cases. The second is a two-dimensional, transonic, viscous optimization problem using a RAE 2822 airfoil. The first is a two-dimensional, transonic, inviscid, non-lifting optimization of a Modified-NACA 0012 airfoil. This study examines two test cases proposed by the AIAA Aerodynamic Design Optimization Discussion Group. Adjoint-based optimization techniques are employed on airfoil sections and evaluated in terms of computational accuracy as well as efficiency. "The primary focus of this work is efficient aerodynamic shape optimization in transonic flow.
